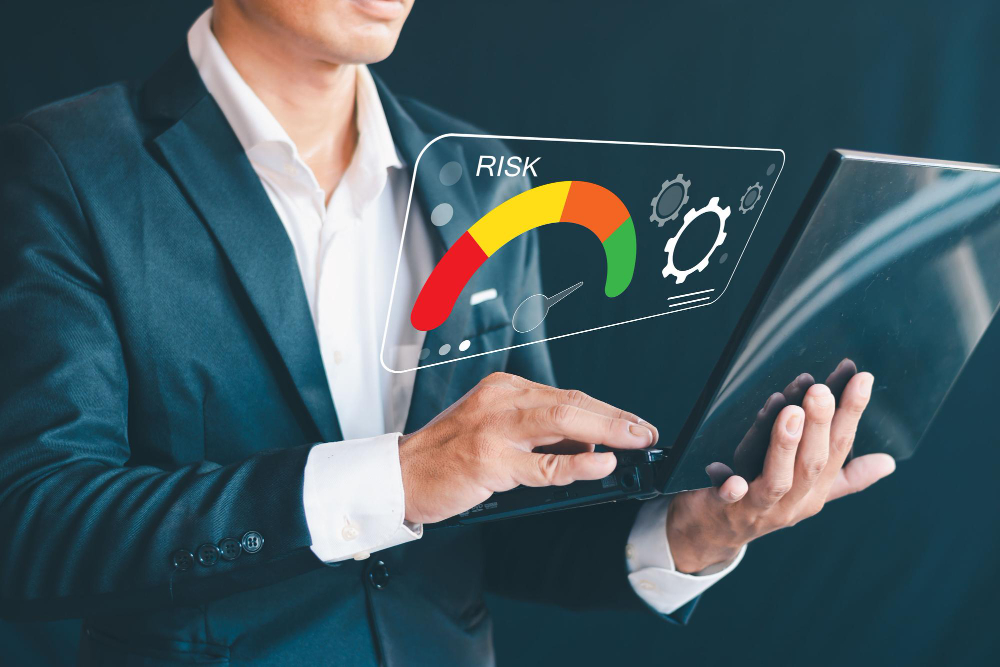
Laboratories are critical spaces for scientific discovery, education, and innovation, but they also come with inherent risks. From chemical spills to equipment malfunctions, a variety of potential hazards can threaten the safety of lab workers and compromise research outcomes. Proper lab risk management is essential to minimize these risks, ensuring that safety protocols are followed and hazards are controlled effectively. This article explores how to identify and manage potential hazards in a laboratory environment, focusing on best practices for lab risk management.
Understanding Lab Risk Management
Lab risk management refers to the systematic process of identifying, assessing, and controlling potential hazards within a laboratory to ensure the safety of workers, protect valuable research materials, and prevent environmental contamination. Effective risk management in the lab involves a combination of proactive planning, hazard identification, risk assessment, and continuous safety monitoring.
The goal of lab risk management is to prevent accidents and mitigate any potential damage or injury that could occur. By integrating risk management strategies into everyday laboratory practices, labs can operate more efficiently and with greater safety, fostering a productive research environment.
Identifying Potential Hazards in the Lab
The first step in reducing risks is identifying potential hazards that could arise within the laboratory. Labs may host a variety of hazardous materials, equipment, and processes, each presenting unique risks. Common laboratory hazards include:
Chemical Hazards
Chemicals are one of the most significant risks in a laboratory. They can cause burns, poisoning, explosions, or respiratory problems if handled improperly. Hazards include corrosive substances, volatile chemicals, flammable materials, and toxic agents. Ensuring proper storage and labeling, as well as appropriate handling procedures, is essential.
Biological Hazards
Many laboratories work with micro-organisms, bacteria, viruses, or other biological agents. Exposure to these organisms can result in infections or allergic reactions. Biosafety protocols must be followed to contain and neutralize biological hazards, such as using personal protective equipment (PPE) and biological safety cabinets.
Physical Hazards
Laboratories often involve complex equipment, hot surfaces, high-pressure systems, and moving machinery. Physical risks like burns, cuts, electrical shock, or falls are common. Lab workers should be properly trained to use equipment safely and should always maintain a clean and organized workspace to prevent accidents.
Ergonomic Hazards
Lab workers may spend long hours conducting repetitive tasks, which can lead to musculoskeletal disorders and eye strain. Proper workstation design, ergonomic training, and regular breaks can help reduce these risks.
Fire and Explosion Hazards
Flammable materials, open flames, and electrical equipment all present fire and explosion risks in a laboratory setting. It is crucial to have fire safety equipment on hand, including fire extinguishers, sprinkler systems, and fire blankets. Regular fire drills and proper handling and disposal of flammable materials are also essential practices.
Radiation Hazards
Some laboratories work with radioactive materials or equipment that emits ionizing radiation. Exposure to radiation can cause significant health problems, including cancer. Labs handling radiation must adhere to strict safety standards, monitor exposure, and use appropriate shielding and containment methods.
Psychosocial Hazards
High-stress work environments, tight deadlines, and potential isolation in some laboratory settings can lead to mental health issues, including anxiety and burnout. Labs should promote a supportive atmosphere where workers feel comfortable addressing stress and mental health concerns.
Erroneous lab results
Erroneous lab results due to expired materials and poor inventory management are significant hazards in the laboratory. Expired chemicals, reagents, or biological materials can degrade over time, leading to inaccurate or unreliable results, such as incorrect reactions or misdiagnoses. Additionally, ineffective inventory management may result in the unavailability of essential materials, improper storage conditions, or confusion about supplies, which can increase the risk of contamination, waste, or accidents.
Risk Assessment: Evaluating the Likelihood and Impact of Hazards
Once hazards have been identified, it’s important to assess the potential risks they pose. Risk assessment in a laboratory involves evaluating the likelihood of each hazard occurring and the severity of its impact. This helps prioritize safety measures and focus on the most critical risks. Risk assessment involves:
- Hazard Identification: Listing all potential risks (e.g., chemical spills, biological exposure, electrical shock).
- Risk Evaluation: Determining the probability of an incident occurring and the potential severity of its consequences.
- Risk Prioritization: Ranking risks based on the likelihood of occurrence and severity to allocate resources appropriately.
A qualitative or quantitative risk assessment process should be part of the overall lab risk management plan to ensure that the highest-priority risks are controlled first.
Integrating Lab Risk Management with Lab Workflow Management Software
As laboratory environments become increasingly complex, integrating Lab Risk Management with LIMS Software can be an effective approach to enhance safety, streamline operations, and mitigate potential hazards. Workflow management software in a lab setting not only facilitates the optimization of laboratory processes but also plays a pivotal role in identifying, managing, and mitigating risks by providing a central hub for safety protocols and data management. Here’s how this software helps improve lab risk management and overall safety:
1. Centralized Hazard Identification and Risk Assessment
Lab management software serves as a centralized platform where lab workers can document, track, and update information related to hazards and potential risks. By integrating Hazard Identification and Risk Assessment into the software, lab managers can ensure that potential risks are immediately flagged.
2. Standard Operating Procedures (SOPs) and Compliance
One of the core features of this software is the ability to organize and enforce Standard Operating Procedures (SOPs) and safety protocols. When workers follow SOPs for risk-prone tasks, the chances of accidents and hazards are significantly reduced.
3. Improved Personal Protective Equipment (PPE) Management
Lab workflow management software can also aid in managing the proper use of Personal Protective Equipment (PPE), which is crucial to minimize exposure to hazards.
Training and Certification Tracking: The software can also maintain records of worker training and certifications related to the use of PPE, ensuring that only trained personnel perform tasks requiring specialized safety equipment.
4. Training and Skill Development
Regular training is critical for lab safety, and workflow management software can enhance Training and Skill Development.
Safety Training Integration: The software can incorporate training modules related to lab safety, chemical handling, and emergency procedures. Lab managers can track which workers have completed training and ensure they stay updated on the latest safety practices.
Automated Reminders: Workflow management software can send automated reminders to staff about upcoming safety training or refresher courses. This ensures workers are continually educated on safety protocols, minimizing human errors that can lead to accidents.
5. Equipment and Maintenance Monitoring
Lab equipment is a vital aspect of a safe and functional workspace. Malfunctioning equipment can introduce significant safety hazards. Lab workflow management software can assist in Equipment and Maintenance Monitoring.
Preventive Maintenance Scheduling: The software helps schedule and track routine maintenance for critical lab equipment, ensuring that all machinery operates properly and reduces the risk of malfunctions that may lead to accidents or failures.
Equipment Calibration and Safety Checks: The software can remind lab staff to perform regular safety checks and calibrations on equipment. By automating these processes, the software ensures that equipment is always functioning within safety parameters, thereby reducing risk.
6. Chemical Management
Lab management software simplifies chemical management by tracking reagents and solutions, ensuring accurate records of their concentration, composition, and batch numbers. It monitors chemical usage in real time, recording details like the purpose, amount used, and which user or department is involved, helping reduce waste and improve efficiency. The software also tracks expiration dates and sends alerts when solutions are nearing expiry.
Additionally, it helps maintain optimal inventory levels by notifying users about available space and predicting how much needs to be ordered for the upcoming week or month based on usage data. This comprehensive approach streamlines operations and ensures a steady supply of chemicals.
7. Collaboration and Communication
Efficient Collaboration and Communication are key to managing risks in a lab environment. Workflow management software improves communication across the team, fostering a culture of safety.
Centralized Communication Hub: The software can provide a shared platform where lab personnel can communicate about potential risks, incidents, or safety updates. This centralized approach ensures that important safety information is disseminated to everyone in real time.
Collaborative Risk Management: Lab managers can collaborate with lab staff to discuss risks, identify mitigation strategies, and review safety protocols. The software supports team efforts in reducing hazards and continuously improving lab safety.
Conclusion
Lab workflow management softwarenot only streamlines day-to-day operations but plays an essential role in enhancing lab risk management. By integrating safety protocols, training modules, equipment monitoring, and real-time incident reporting, these systems provide a holistic approach to reducing risks and improving lab safety. With a well-implemented workflow management solution, laboratories can proactively manage hazards, minimize incidents, and maintain a safer environment for workers and researchers alike.
Ultimately, integrating lab risk management with workflow management software creates an intelligent, data-driven safety culture where risks are minimized, compliance is ensured, and lab operations run smoothly and efficiently.